지난 14일 전남 광양시 국가산업단지 명당3지구 포스코 풀필먼트센터(보관·배송·반품 등 물류 서비스를 총괄하는 일괄 물류센터). 직원이 태블릿PC로 ‘측정’ 버튼을 누르자 3차원(D) 스캐너가 정사각형 모양의 노란색 판 위에 놓인 부품(배관)의 크기와 무게를 측정했다. 스캐너로 중량이 114kg인 것을 확인된 후, 작업자가 태블릿PC 내 버튼을 누르자 ‘스태커 크레인’으로 불리는 로봇이 주문 빈도를 고려해 ‘셀(선반)’로 부품을 옮겼다.
◇ 자재 크기 별로 로봇이 운송해 저장
풀필먼트센터에서는 로봇들이 최적의 물류 이송 경로에 따라 자재들을 저장한다. 현업 부서에서 필요한 자재 배송을 요청하면 최대 아파트 10층 규모인 28.5m에서 물건을 집어 작업자에게 전달한다. 작업자가 로봇이 꺼내온 물건을 집어 AGV(무인운반로봇)에 올리면, 최대 1톤까지 운반 가능한 AGV로봇이 이를 출하존까지 옮긴다. 이 과정은 모두 포스코DX와 포스코가 자체 개발한 ACS(AGV Control System)에 의해 운영된다.
포스코DX 관계자는 “제조업에서 모든 물류 과정을 자동화한 곳은 포스코 풀필먼트센터가 최초”라면서 “사람이 하는 일은 태블릿PC로 작업 지시를 내리고 로봇이 운송하는 부품을 옮겨 실어주는 게 전부”라고 했다. 로봇이 대부분의 작업을 담당하다 보니 축구장 7개를 합친 크기인 5만㎡ 규모의 풀필먼트센터에 근무하는 사람은 약 12명에 불과하다. 포스코는 제철소에서 필요한 자재 조달을 효율적으로 하기 위해 기존 300여개 창고에 분산됐던 물건들을 풀필먼트센터에 모았다.
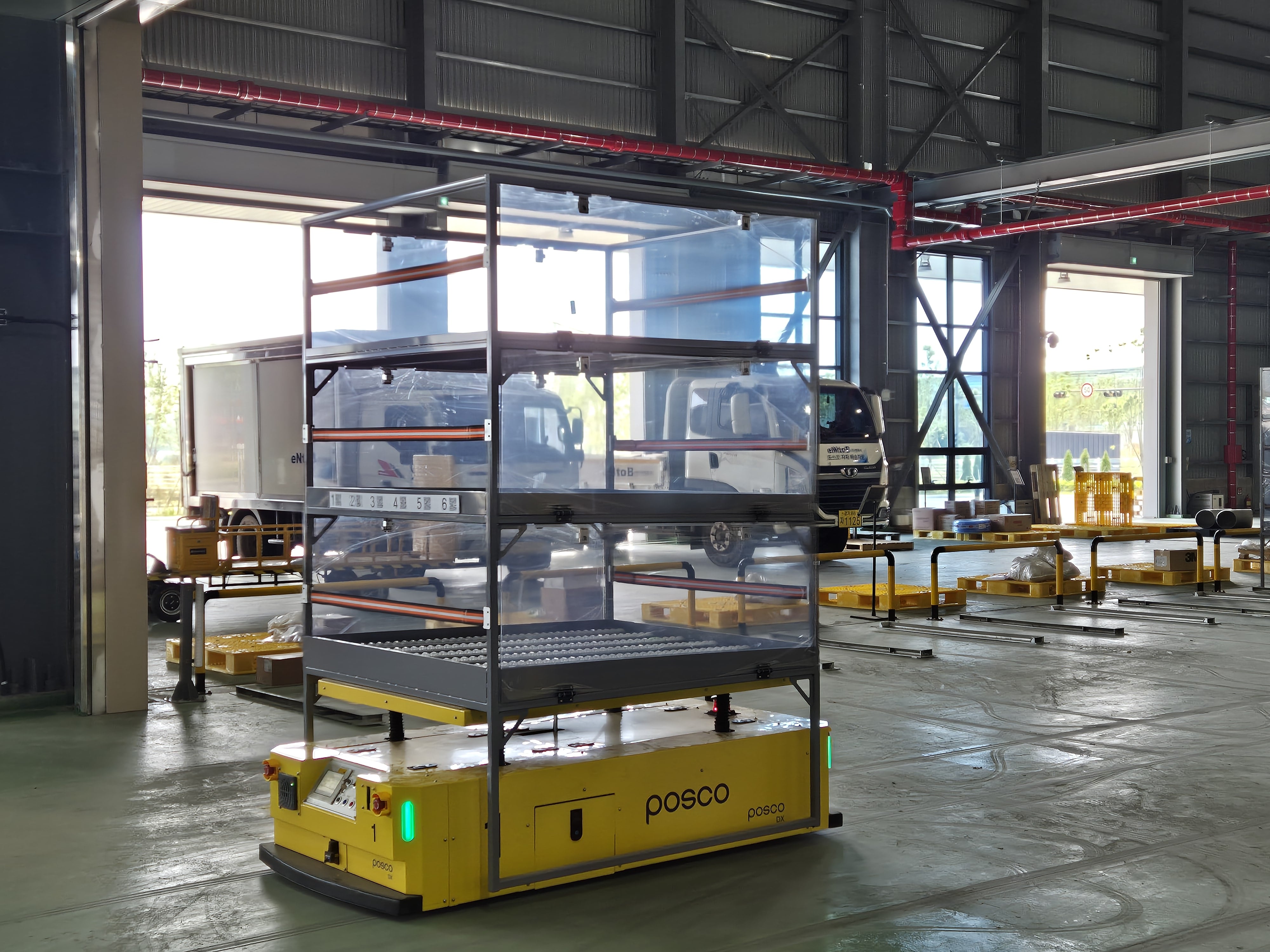
이곳에서 물건은 크기에 따라 총 3곳으로 나뉘어 보관된다. 30kg 미만의 소형 자재들은 큐브형 창고인 ‘오토스토어(Auto Store)’로 이송된다. 이곳에서도 로봇들이 최적의 물류이송 경로에 따라 자재들을 이송한다. 포스코DX 관계자는 “오토스토어는 입·출고존으로 나뉘는데, 주문 빈도가 높은 자재들은 출고존과 가까운 곳에 저장된다”고 말했다. 30kg 이상 1톤 미만 자재들은 입체자동화창고에, 1톤 이상 5톤 미만 자재들은 대형 적치대에 보관된다.
포스코DX와 포스코는 자재 수요를 예측하고 재고를 관리하는 WMS(창고관리시스템)도 함께 개발했다. 직원들은 WMS을 통해 풀필먼트센터에 가지 않고도 자재의 위치와 상태를 3D 메타버스를 통해 조회하고 주문할 수 있다. 태양광 발전 설비를 통해 전력을 자체 조달하는 점도 풀필먼트센터의 특징이다. 이곳의 발전 용량은 1.4메가와트(MW)로 500여 가구가 1년 간 사용할 수 있는 규모다. 포스코는 자체소비 후 남은 전력을 향후 외부에도 판매할 예정이다.
◇ 고위험 공정도 AI·로봇으로 안전하게
포스코DX는 제조 현장에 특화된 산업용 인공지능(AI)과 로봇을 결합한 인텔리전트 팩토리를 구축하고 있다. 올 들어 산업용 로봇에 대한 컨설팅, 설계, 시스템 구축 등을 전담하는 로봇자동화센터를 신설한 포스코DX는 포스코 광양제철소와 공동으로 아연 도금 공정에 로봇을 활용하는 프로젝트도 진행 중이다. 아연 도금공정에 로봇을 적용하는 프로젝트는 지난 2021년 12월부터 지난 5월까지 총 8개 공장에 적용된 상태이다.
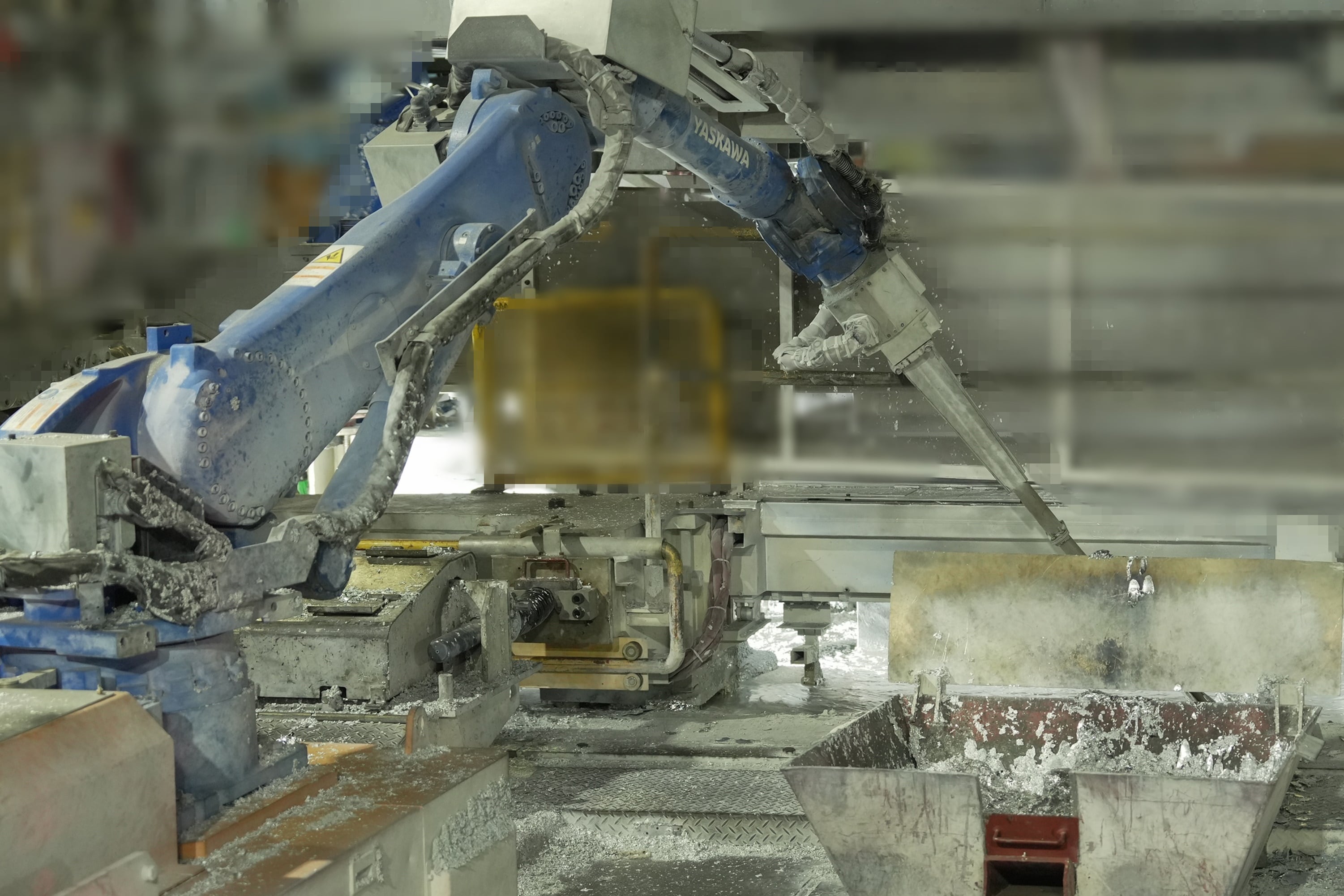
이날 포스코 광양제철소 4도금 공장에 들어서자 뜰채가 달린 팔로 포트에서 은색 액체를 퍼내는 로봇이 눈에 들어왔다. 이곳은 철판 표면에 아연을 입히는 공장인데, 도금 공정에서는 아연이 녹아 있는 고온의 포트 속 이물질을 제거하는 작업이 필수적이다. 그동안 섭씨 460℃에 달하는 포트 옆 비좁은 공간에서 작업자 4명이 한 조가 돼 하루에 10번씩 이물질을 직접 긁어냈다. 포트가 뜨거운 만큼 화상 등의 사고 발생 가능성이 있는 고위험 현장이었다.
AI와 로봇 기술이 적용되면서 도금 공정은 사람 손을 거치지 않게 됐다. 포트 주변에 설치된 카메라를 통해 비전 AI가 포트 내 이물질 분포를 분석하면, 2m 높이의 로봇이 팔을 움직이며 불순물을 제거한다. 아연 도금을 마치고 품질 검사까지 끝낸 철판은 두루마리 휴지처럼 말린다. 상품 출고 전 라벨링 작업에도 로봇이 투입되는데, 통합생산관리시스템(MES)과 연동된 로봇이 제품의 생산 정보가 담긴 라벨을 붙인다. 로봇 적용으로 오배송 위험이 사라졌다고 포스코는 설명했다.
윤석준 포스코DX 로봇사업추진반장(상무)은 “산업용 로봇은 로봇만 구매해 들여놓는다고 끝나는 게 아니라, 로봇이 효율적으로 쓰이도록 시스템을 설계하고 구축해야 자동화에 따른 이점을 얻을 수 있다”면서 “포스코DX는 로봇 하드웨어를 공정에 맞게 제어하고, 소프트웨어 측면에서는 3D, AI 등의 ICT 기술로 로봇의 고부가가치 역량을 확보하는 데 차별화를 두고 있다”고 말했다.
- [현장의 시각] 권도형 美 벌금 6조와 韓 금융 당국의 직무 유기
- [기자수첩] 예·적금보다 못한 보험사 연금 상품
- 삼성전자, 글로벌 전략회의서 모바일·반도체 등 ‘새 판 짜기’… 키워드는 AI·수익성
- 애플, 미국서 ‘선구매 후지불’ 대출 1년여 만 중단
- HD현대중공업, 3200t급 필리핀 초계함 ‘미겔 말바르함’ 진수